WHAT JOBY AVIATION LEARNED FROM TESLA - BATTERIES, CHARGING, COOLING
- Osinto HQ
- Jan 13, 2023
- 10 min read
Updated: Jul 26, 2024
BACKGROUND
Joby Aviation are developing electric vertical takeoff and landing / eVTOL aircraft. Two of their pre-production 'S4' experimental prototype airframes have been registered with the FAA - N541JA Serial #JAS4-101 and N542BJ Serial #JAS4-202 (one of which was damaged in a crash last year) - as well as a sub-scale 55lb / 25kg Unmanned Aerial Vehicle / UAV:
Following a merger with LinkedIn co-founder Reid Hoffman's Special Purpose Acquisition Company / SPAC in 2021 the company are publicly listed (NYSE: JOBY). We've used a combination of information shared by the company themselves (press releases, job ads, blog posts etc.), excerpts from media coverage, alongside SEC and patent filings to investigate Joby's approach to batteries, charging and cooling of their electric aircraft.
Their July 2021 investment memo is a key document in researching the business:
In it Joby reveal that:
"Each propeller is powered by two independent electric motors, each in turn driven by independent electric motor drive-units. Each drive-unit draws power from a separate battery, of which there are four onboard the aircraft"
BATTERIES AND VERTICAL INTEGRATION
Slides in the investment memo show example battery pack locations in the aircraft's wings / forward nacelles:

This seems to still be the case - stills taken from a December 2022 YouTube video posted by Kirsten Dirksen recorded at Joby's facilities spread across Marina Municipal Airport (a former US Army airfield in California) show charging and cooling connections affixed to similar locations on the aircraft:
THE TESLA CONNECTION
Joby Aviation CEO JoeBen Bevirt hired Tesla veteran Jon Wagner back in 2017 to head up powertrain and electronics. Wagner was "team leader for battery pack design engineering" at Tesla, a role which included work on the battery packs in the Model S/X, Model 3 and Powerwall:
Wagner's experience included work on "mechanical, thermal, structural, electrical, and system engineering" and he has introduced a similar set of in-house capabilities at Joby - setting it apart from competitors.
This vertically integrated approach is harder, more capital intensive and requires the recruitment of a diverse and highly skilled workforce, but the tight integration of design and manufacture can yield significant performance and speed advantages once the requisite labour force, facilities, equipment and processes are in place. Joby are likely to be able to iterate quicker than the competition - mimicking an approach that has been so successful at Tesla and SpaceX.
Whereas Archer Aviation (Source), SkyDrive (Source) and Supernal (Source) have, in the short-term at least, elected to procure integrated battery modules from Utah's Electric Power Systems, Joby are procuring battery cells and then designing, engineering and testing the packs and modules that contain them, in-house:
One way that Joby says it’s achieved its performance goals is by building practically all of the aircraft in-house apart from the battery cells
Source: Forbes, Nov. 2020
Here's a brief glimpse of Wagner talking to Andersson Cooper about Joby's batteries in a segment on 60 Minutes:
A Joby patent filing for an Aircraft Propulsion Unit / APU from August 2022 (on which Wagner is named) illustrates well the Cell > Module > Pack hierarchy:
Tesla's battery strategy has seen them predominantly source cylindrical form factor lithium ion battery cells. Much of that supply in the US has been from factories co-developed with long-term partners Panasonic, though increasingly they source around the world from a range of suppliers - the Shanghai factory permissions likely coming with a stipulation for local supply (provided by li-ion global market behemoth CATL).
Previously having favoured steel encased cells measuring 18 x 650mm or 21 x 70mm (referred to as 18650s or 2170s respectively) Tesla are transitioning to a larger form factor 48 x 60mm or '4860' cell, developed with Panasonic. This could be considered the cutting edge of mass-produced li-ion battery cells.
The electric vehicle industry also use lithium ion cells in pouch and prismatic form factors, a selection of which can be seen below:
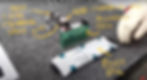
WHAT WE KNOW ABOUT JOBY'S BATTERY STRATEGY
Joby will initially use cells already in production for automotive use
They'll start with 811 NMC cathode, graphite anode cells
The S4 batteries are liquid-cooled, both on- and off-aircraft
Joby want to leave their options open to swap in alternative batteries / power sources in future
Joby and third party sources have made multiple references to using batteries already in high volume production eg. for electric cars - reducing technology risk and hoping to smooth the path to certification of their aircraft for passenger-carrying commercial work on which their business plan depends:
The automotive cells he’s using pack “almost” 300 watt-hours per kilogram in specific energy, Bevirt says, well short of battery chemistries under development promising 400 Wh/kg and up that some other electric VTOL developers appear to be waiting for to make their aircraft viable.
Source: Forbes, Nov. 2020)
Chairman Paul Sciarra said in an interview with IPO Edge:
"...certainly batteries and the progression of batteries will continue. The target that we set for ourselves is look, we’ve got to be able to hit these specifications with batteries that are already in high volume, high quality production for another application now.
We did not want to be in a scenario, John, where we were trying to pull brand new batteries out of the lab and onto the manufacturing line. That’s a stacking of risk, technical risk on the aircraft plus technical risk in terms of the ability to scale and manufacture battery production. And you know, that double risk felt like one that was not worth taking.
So, getting back to your point, we do think that there are going to be opportunities to take advantage of improvements in batteries over time. And we think there may be opportunities to even do a, what’s called a sort of supplemental certification, to our initial type certification of the vehicle, that would certify new battery packs that would basically go into what would otherwise be the same vehicle, to really begin to take advantage of those progressive improvements in energy density over time."
(Source: SEC Filing, July 2021)
In a July 2021 Press Release Joby confirmed that their prototype aircraft:
"...uses commercially available lithium ion batteries that have been adapted for aerospace use. An 811 NMC cathode and a graphite anode cell were selected, following internal testing..."
(Source: Joby Aviation, July 2021)
811 NMC CELLS
811 NMC lithium ion battery cells are a relatively high energy density cell chemistry that stand up well to high numbers of charge cycles, but are a little more thermally unstable and hence 'less safe' than other available li-ion cell chemistries - hence the need for well managed cooling during charge and discharge cycles.
NMC 811 is the cell chemistry favoured by Tesla for their longer range and higher performance model variants. The cathode comprises of nickel, cobalt and manganese in a ratio of 8:1:1 - it's quite brittle and (in Tesla's latest 4680 cells at least) bonded to an aluminium film:
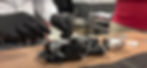
The graphite anode is typically bonded to a copper strip:
Most major li-ion battery manufacturers now have an 811NMC offering in one form factor or another - from smaller players like Germany's Custom Cells and China's Grepow to major volume producers like CATL, Panasonic Energy and SK On.
WHAT JOBY MIGHT BE DOING
If Joby's approach does mirror that of Tesla we'd expect them to procure cells made in the US (with a high % of US derived mineral content as per Inflation Reduction Act incentives) - and to then integrate those cells into packs and modules in-house. We initially thought this might be at their planned Marina production facility (see the planning application for Joby's Marina facility in full here):

Since first publishing this post we received a suggestion to check the location of battery-related job vacancies at Joby and doing so confirms that battery, powertrain and power electronics positions all list the company's facility in San Carlos, California as the place of work. As such it seems a safe bet that cells are integrated into packs at this location, not at Marina as we first posited:
We'd expect Joby to be working directly with battery manufacturers on future cell types, and it might be that a prismatic or pouch cell is being considered, but we suspect they'll have started out with a 2170 Tesla/Panasonic cylindrical cell or similar.
Indeed a patent filing dated October 2022 for a Battery Thermal Management System and Method naming Wagner alongside fellow Tesla battery veteran Ernest Villanueva (a battery module design specialist) indicates that the company are at the very least keen to protect system architectures that might include cylindrical as well prismatic / pouch cells:
WHO IS JOBY AVIATION'S BATTERY SUPPLIER?
Given Joby Aviation's involvement with the US Department of Defence - including participation in the US Air Force's Agility Prime programme which has a stated goal of securing strategic eVTOL supply chain capability on US soil - we believe it unlikely Joby would select a Chinese cell supplier, nor one who lack US-based cell manufacturing capacity. At the very least their volume supplier would need to have demonstrable plans to establish / increase a US manufacturing footprint to supply a production line of eVTOL aircraft.
We go more in-depth on lithium ion battery manufacturers and their plans for US production here - including taking a look at Joby Aviation investor Toyota's progress on a li-ion battery cell manufacturing facility in North Carolina - we'd suggest this could be a likely candidate for volume cell production supply to Joby, if the two EV specific production lines are up and running in time c. 2025.
The majority of the world's 10 largest battery companies can likely be ruled out on the basis that they are either Chinese or have the majority of their manufacturing capacity in mainland China - leaving us with Japan's Panasonic Energy and SK On as possible candidates from the global top ten. Given Panasonic's tie-up with Toyota on prismatic cell production in North America - read more on the Prime Planet Energy JV here - and their history of working with Tesla, we'd say Panasonic are the most likely candidate to supply Joby with battery cells in the near-term, with a view to procuring in greater volumes from Toyota's under construction US battery facility in North Carolina.
It's reported that Joby scoped sites for their manufacturing facility across the US, including in North Carolina, for their aircraft manufacturing site under the codename 'Project Aniram', before settling on Marina Municipal Airport in their native California.
Given that Toyota's $2.5bn USD investment in a li-ion battery manufacturing facility is also located in North Carolina, it seems obvious that the companies would be, at the very least, coordinating future battery strategy and that cell supply from the under-construction Toyota plant in NC has at the very least have been under serious consideration.
LI-ION BATTERY COOLING
Tesla fuse their batteries together into packs / modules (most recently using polyurethane foam) with 'micro channel extrusions' running between them, through which a liquid coolant runs, channeling heat away from the sides of the cells. It's not the *best* solution as cylindrical cells reportedly heat up most at the top and bottom, but it works:

Managing thermal runaway can be an issue with li-ion cells - particularly as they can also expand and contract slightly when under high charge or discharge loading. In electric car battery packs an elegant solution has been adopted by Tesla:
The top of the battery module container is made from a strongly heat resistant metal (steel we believe), which functions like an aircraft's firewall, forming a strongly heat resistant barrier between the passenger cabin and the batteries in the event of fire
The bottom is instead made from aluminium, so that in the event a cell / multiple cells start venting material this base will sacrificially melt and the cells can simply drop onto the ground where fire crews can more easily extinguish them, and away from the rest of the battery pack, occupants etc.
Ejecting burning batteries from an eVTOL aircraft is presumably *not* an option! We suspect much of the work being undertaken by Wagner and his team at Joby will be on the packaging around the cells and managing thermal loading / runaway to the satisfaction of the FAA's certification teams.
Bevirt is quoted as saying that their vertical integration includes the metallics used in some of the aircraft’s components, which are machined and manufactured in Germany (see our July 2020 scoop on Joby's establishment of a Munich operation in close proximity to competitor Lilium) - this might well include elements of battery housing / packaging:
“That manufacturing team of engineers in Munich are the ones that are doing that work and making those parts efficiently and cost-effectively” [Source].
A 2020 article in Aviation Week indicated that the battery packs in its eVTOL would have onboard liquid cooling, which should help keep them at a constant desired temperature during discharge [Source].
For recharging, Bevirt said during an IPO Edge webinar the company will be using proprietary chargers “that do both the charging and the thermal management of our battery system while we’re charging, and that allows for a very rapid charge rate and a very rapid turnaround time that’s on the order of the time that it takes for us to unload one set of passengers and load the next.”
We recently caught a glimpse of that charging setup from the October 2022 patent filing in a YouTube video tour of Joby's facilities at Marina Municipal Airport in California:
IN SUMMARY
Joby Aviation have confirmed their intention to use lithium-ion cells already in large-scale production for automotive applications, to reduce risk
The company have publicly stated that their preferred cell chemistry is an NMC 811 cathode combined with graphite anode - a high energy density chemistry used by Tesla
In the short-term, for development aircraft, Joby are likely to have used the same cylindrical cells found in most Tesla cars - which might have been sourced from Tesla / Panasonic directly or even through the purchase or new / used Tesla vehicles
The cylindrical cells would likely be in 18650 / 2170 (our best guess) / 4680 form factor, are likely liquid cooled with fluid flowing between the sides of the cells within the pack / module casing on the aircraft, with additional off-aircraft cooling provided when charging by a bespoke, patented, on-ground charging apparatus
Joby are forming the cells into bespoke battery modules in-house, which together form larger battery packs, all of which undergo extensive in-house testing and verification
We expect that for volume production Joby might source cells from Toyota Battery Manufacturing North Carolina (TBMNC) whose planned $2.5bn plant is under construction and expected to produce first cells 2024-25
UPDATE 23-01-23 - we noticed that Joby are listed as a partner on Redwood Materials' website - the battery recycling company started by ex-Tesla CTO and co-founder JB Straubel - that's raised nearly $800m USD in funding:
Notably Redwood also have deals inked with both Toyota [Source: Forbes] and Panasonic [Source: CNBC].