TOYOTA'S NEW LITHIUM-ION BATTERY FACTORY IN NORTH CAROLINA - AS SEEN FROM SPACE
- Osinto HQ
- Jan 16, 2023
- 5 min read
Updated: Jul 26, 2024
Toyota - the world's largest carmaker - are generally regarded as something of a laggard in the all-electric vehicle market, having seemingly squandered an early lead established in the hybrid-electric segment:
Reuters: Exclusive: Toyota scrambles for EV reboot with eye on Tesla - October 24, 2022
Forbes: Why Toyota Has Got It Wrong On Electric Cars - October 2, 2021
CNBC: Why Toyota – the world’s largest automaker – isn’t all-in on electric vehicles - September 13, 2022
TOYOTA AND TESLA'S LOVE-HATE RELATIONSHIP
Global President of Toyota Motor Corporation Akiyo Toyoda (great-grandson of illustrious founder Sakichi Toyoda) went as far as publicly criticising Tesla in 2020 - a quite unusual move for the usually conservative Japanese conglomerate.
It's worth remembering that Toyota were early Tesla investors and retained a 3% shareholding in the Californian upstart until the end of 2016 - which with the benefit of hindsight seems unfortunate timing (even given the precipitous 60+% recent fall in Tesla's valuation):

Back in 2010 Tesla proudly announced a partnership with Toyota "on the development of electric vehicles, parts, and production system and engineering support" [Source: Tesla] in a Press Release that saw Toyoda praise Tesla's "challenging spirit, quick decision-making, and flexibility" and Tesla CEO Elon Musk admire "Toyota’s legendary engineering, manufacturing, and production expertise."
(There are reports that the companies are now working together again as of 2022 - though this time with a focus on autonomous driving tech).
TOYOTA'S BATTERY SIPPLY PROBLEM
One of the key bottlenecks facing any company looking to build and sell battery-electric (or hybrid) cars today is the globally constrained supply of lithium-ion battery cells. Though reportedly as much as $300 billion has been invested in battery factories worldwide since 2019 [Source: Benchmark Source], adding up to "3.1 terawatt hours of potential new capacity", competition for supply from existing plants is fierce, as it is for the minerals they consume.
In playing catch-up Toyota are growing their battery cell manufacturing footprint, including in North America through a $2.5bn investment in Toyota Battery Manufacturing, North Carolina (TBMNC) - "owned 90% by Toyota Motor North America, Inc. and 10% by Toyota Tsusho Corporation" - announced in August 2022 and with production targeted to begin "between 2024 and 2026". This comes alongside a c. $3bn investment in Japan for a total of "up to 40GWh" according to Toyota themselves.
Even this announcement - of a $5.6bn investment in battery production on two continents - is caveated with:
"Toyota believes that there is more than one option for achieving carbon neutrality...[and]...will continue to make every effort to flexibly meet the needs of its various customers in all countries and regions by offering multiple powertrains and providing as many options as possible."
Clearly the battery-electric faction aren't in overall corporate control just yet!
TOYOTA'S BATTERY 'MEGASITE' VISIBLE FROM SPACE
The US site lies south-east of Greensboro, North Carolina on the so-called Greensboro-Randolph Megasite. Drone stills from June and timelapse satellite imagery below show construction progress:
It's noteworthy that the Japanese car maker *still* expect the majority of even this plants batteries to find their way into hybrid vehicles - of the six planned production lines four will be dedicated to supplying batteries for hybrid vehicles, and just two for pure battery-electric.
When it comes online in 2025, TBMNC will have four production lines, each capable of delivering enough lithium-ion batteries for 200,000 vehicles—with the intention to expand to at least six production lines for a combined total of up to 1.2 million vehicles per year.
[Source: Toyota]
Satellite imagery of construction progress at Toyota Battery Manufacturing North Carolina / 'TBMNC' as of 29-12-2022:
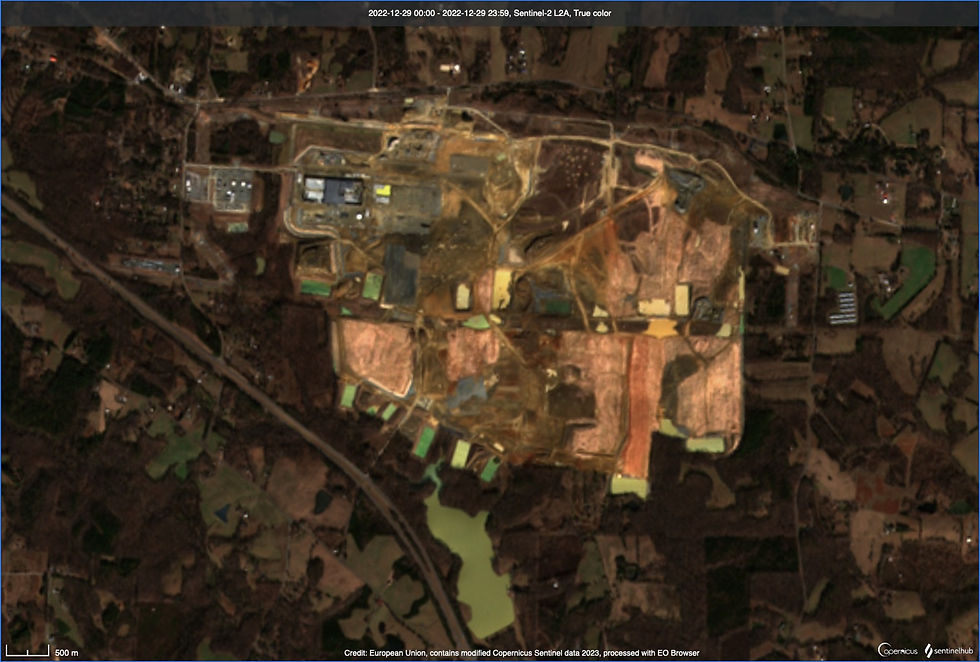
The timelapse below shows construction progress from January to December 2022:
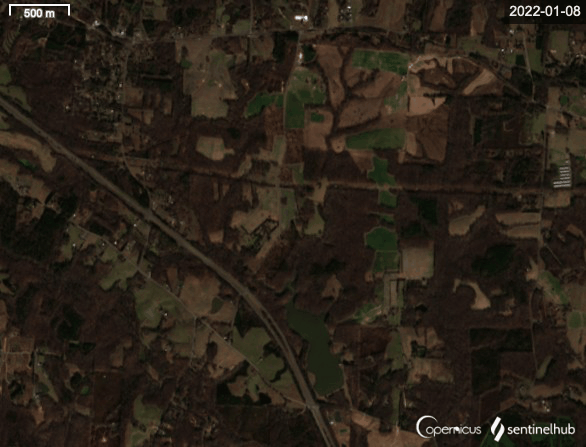
Renders of the completed facility from Toyota Press Release:
SOURCING MINERALS
President Biden's 'Inflation Reduction Act' passed in August 2022 might well have influenced Toyota's decisions on where to source minerals for their US plant. New requirements for electric vehicles and their batteries are aimed squarely at increasing domestic (and/or 'friendly' Nation State) production capacity - presumably to reduce dependence on China, who currently dominate the sector:
"The USA Inflation Reduction Act...requires manufacturers to provide verifiable evidence that large percentages of material sourcing and manufacturing take place within the US or in a partner country with a free trade agreement. Manufacturers must prove that battery components have not been “extracted, processed or recycled by a foreign entity of concern.”
[Source: Everledger]
Japan's Panasonic and Toyota have formed a new Joint Venture (JV) in North America - Prime Planet Energy & Solutions - which has signed a binding 5-year supply agreement for 4,000 tonnes of lithium carbonate annually from ioneer's Rhyolite Ridge project in Nevada - "the largest known lithium and boron deposit in North America" - that's a little under 20% of the projected 20,600 tonnes the Australian company expect to extract form the site. Production however is not expected before 2025-26:
PRISMATIC CELLS IN FAVOUR?
It's worth noting that the Prime Planet Joint Venture focuses quite specifically on prismatic cells (batteries in a rigid, rectangular casing) as opposed to the cylindrical cells preferred to date by Tesla. Many auto makers seem to favour the prismatic form factor - an example of which you can see below - recently produced by the new NorthVolt battery factory in Sweden for Geely-owned Volvo:
The automotive sector as a whole seem to be displaying an increasing preference for the prismatic form factor. Each cell can hold more energy, and there's the potential to move from a cell > module > pack housing hierarchy to a simpler cell > pack packaging method, if the steel casing is sufficiently 'structural'. Such a cell shape also presents a large side surface area for cooling. Prismatic cells have typically been 'bottom-cooled' to date, though that is changing.
Some reports suggest prismatic battery cells already constituted up to 40% of the vehicle lithium-ion battery market in 2020, with pouch cells at c. 35% and the cylindrical format (favoured by Tesla) just 10%. We're looking for more recent data on how that trends developing - email us with any leads.
The world's largest li-ion battery manufacturer - with a 34% global market share (Source: The Visual Capitalist) - are China's Contemporary Amperex Technology Co., Limited / 'CATL'. Their freshest offering for the electric vehicle market is- the 'Qilin' - set to go into production in 2023 - and a good example of a cutting edge battery pack built around prismatic form-factor lithium-ion battery cells:
The Toyota - Panasonic Prime Planet JV have yet to release full details of their prismatic cell offering aside from these concept images from their website:
We're working up a market map to show how the top battery suppliers and automakers are connected - get in touch if you've an interest in that piece of work.
Comments